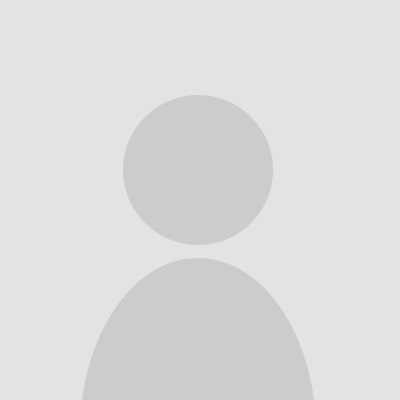
Prabhu Ram, Head – Industry Intelligence Group
From Simulation to Success: How Digital Twins are Reshaping Manufacturing
The rapid advancement of technology has paved the way for transformative innovations in various industries, and manufacturing is no exception. In recent years, trends such as digital twins have been reshaping the manufacturing landscape. By bridging the physical and digital realms, digital twins enable manufacturers to optimize processes, enhance productivity, and drive innovation.
As advancements in connectivity, data analytics, and AI continue, digital twins are poised to reshape the future of manufacturing, empowering organizations to stay competitive in an increasingly dynamic and demanding market.
With companies like Flex at the forefront of these developments, the potential for optimization, efficiency, and agility in manufacturing operations has reached unprecedented levels.
I recently spoke with Glen Tan, Senior Vice President, Global Operations, at Flex. We dived-deep into the opportunities that digital twins provide, the challenges involved in integrating digital twins, and the opportunities that the future holds.
Digital Twins: Bridging the Physical and Digital Worlds
One of the key technological trends in manufacturing is the concept of digital twins. A digital twin serves as an exact replica or model of the physical world, providing real-time visibility and insights into various processes. By feeding relevant data sets into the digital twin, organizations can simulate different scenarios, optimize processes, and gain valuable insights without the need for physical trial and error. The result is improved cycle time, enhanced quality, and cost reduction. The data incorporated into digital twins can span from environmental factors like temperature and humidity to physical attributes such as weight, dimensions, and even financial data.
Enhancing Agility and Operations with Digital Twins
Digital twins offer significant advantages by increasing agility and bolstering operations in manufacturing. By iterating through countless “what if” scenarios, organizations can save valuable time and costs. Production line issues can be identified and resolved before physical implementation, and potential bottlenecks throughout the product lifecycle, from design to logistics, can be eliminated. A compelling use case is exemplified by Flex’s collaboration with a medical device customer in the launch of a new Class II diabetes product. By leveraging digital twins, the product model underwent iterative refinement, reducing the time-to-market from months to weeks. Moreover, optimization of scheduling enabled Flex to exceed customer expectations by producing 8.1 million units per quarter instead of the projected 5.5 million.
Increasing Flexibility in Production Planning
Production planning is a critical aspect of manufacturing that requires optimization of resources such as labor, machinery, and materials. Digital twins provide a powerful tool to determine the optimal output based on desired outcomes, whether it’s revenue maximization or quantity optimization. The traditional trial-and-error approach is streamlined, enabling manufacturers to respond more swiftly to changes in demand or resource availability.
Benefits of Digital Twins for Manufacturers
The adoption of digital twins brings several significant benefits to manufacturers. Foremost, it offers unparalleled speed and quality by visualizing outcomes before physical implementation. By identifying potential issues and optimizing processes in the digital realm, manufacturers can drive business growth, increase profitability, and improve cash flow.
Integrating Automation with Human Labor
While automation technologies play a crucial role in driving efficiency and quality, human workers remain integral to the manufacturing process. Flex acknowledges the importance of human intervention in interpreting information and making critical decisions. For instance, simulation and digital twins can guide design changes for manufacturability, but factors such as cost and time-to-market considerations necessitate human involvement. Flex adopts a gradual approach called “autonomation,” where automation is introduced to specific steps while preserving human involvement, facilitating smoother workforce development and transformation.
Challenges in Deploying Digital Twins
The deployment of digital twins comes with its own set of challenges. A successful digital twin deployment must align with business objectives and provide measurable impact. Establishing a functional, real-time digital twin simulation requires a vast amount of data from various processes and sources, demanding a robust data management infrastructure. Significant investments in data collection, connectivity, and storage may present hurdles for some organizations, making it imperative to bridge existing gaps in data streams and digitize assets and processes for real value realization.
The Future of Digital Twins: A Global Perspective
We have now reached a tipping point in the manufacturing industry, leveraging Industry 4.0 technologies to accelerate innovation and growth. With over 1,000 simulation projects completed, Flex has demonstrated the transformative potential of digital twins in manufacturing.
Looking ahead, the future holds promising advancements as technology continues to be harnessed for better product development, improved employee experiences, and enhanced operational efficiency. The integration of cutting-edge technologies such as digital twins, artificial intelligence, and machine learning will continue to shape the global manufacturing landscape.
Conclusion
Digital Twins represent an exciting new chapter in the manufacturing industry.
Companies like Flex are spearheading this revolution by harnessing the power of digital twins to optimize processes, enhance agility, and drive business growth. As organizations integrate automation technologies with human labor, they pave the way for a harmonious collaboration that leverages the strengths of both. While challenges in deploying digital twins exist, the future remains bright, with Industry 4.0 technologies poised to shape the global manufacturing landscape. With continuous innovation and the transformative potential of digital twins, manufacturers can embrace a future of unprecedented efficiency, optimization, and competitiveness.