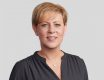
The COVID-19 pandemic has truly tested the resilience of global supply chains. Over the past year and more, the pandemic has exposed vulnerabilities in a complex, and inter-connected global economy. The pandemic forced enterprises to adapt and adjust their operations to dynamically respond to ever evolving demand and supply requirements.
Flex operates one of the most complex supply chains in the world with 16,000 direct suppliers and >1Mn SKUs. I recently managed to have some time with Lynn Torrel, Chief Procurement and Supply Chain Officer at Flex, to understand the current state of play, the pandemic playbook at Flex, especially, the resilience of its supply chains, and the implications of the ongoing moves towards regionalized supply chain hubs, amongst others.
Lynn Torrel is responsible for direct and indirect materials, transportation and logistics, business operations, materials management and strategic supply chain management at Flex.
Key lessons for supply chain management
We have reached a tipping point to re-engineer our end-to-end supply chains at scale. Even before the pandemic, powerful environmental, technological and political forces were already feeding an appetite to redesign corporate strategies and operations. The geopolitical undercurrents against open trade that preceded COVID-19 were motivating businesses to find ways to manage tariffs and other government-imposed cost regimes. Add to this the alarm bells that scientists and researchers have been sounding about various global risks which may finally be heeded in the wake of COVID-19 – and you have the ripest conditions yet to overcome entrenched human behavior and force a restructuring of corporate value chains at scale.
If the pandemic has taught supply chain managers anything, it is that over-dependence on any one partner, country or region can lead to critical issues and challenges. A diversified supplier base will usually cost more than a consolidated one; likewise, migrating a supply chain to regional markets also requires a hefty upfront investment. Yet the tradeoffs between security and costs must be weighed and failure to adapt in today’s highly dynamic world could lead to poor outcomes with dire financial consequences.
Given our increasingly complex and interconnected world, sudden shocks are more probable than ever. Every 3.7 years on average, businesses can expect a supply chain disruption that lasts at least a month, and the most serious of these can have severe financial consequences, according to a 2020 McKinsey analysis.
This forecast coupled with present trade barriers and imminent global risks presents an opportunity to take proactive measures. Devising a continuity plan before the next disaster strikes can help minimize supply chain disruption. Managers would also do well to assess their top risks and understand the corresponding risk profiles for each supplier. Businesses can take steps to earnestly plan for black swan events, capitalizing on the fresh lessons learned from COVID-19 to explore alternative ways forward.
Flex’s playbook for supply chain management
Flex operates one of the most complex supply chains in the world with 16,000 direct suppliers and over 1 million SKUs. Our response to COVID-19 validated the work Flex started over five years ago to combine technology and data and enable employees to make smart strategic decisions regarding the supply chain. A big advantage for us is our Flex Pulse system. This is a home-grown software-based real time mobile collaboration tool providing unprecedented levels of connected intelligence for managing global supply chains. This system has been globally recognized as one of the very best at improving supply chain performance.
But you can’t live on data alone. You also need a team of skilled supply chain professionals that can interpret the data and combine it with their own industry knowledge to make decisions. Flex has over 10,000 supply chain professionals and they played a pivotal role in aligning the entire supply base from demand, through material planning and procurement, to customer delivery. Early in the pandemic we established cross functional teams and held daily calls to discuss what was a very dynamic situation. I made sure every member of the team was heard and we adopted the phrase Discuss, Debate and Decide. We could not become paralyzed by the data or the situation. In the end, we were successful because of both the data and supply chain professionals combining it with their knowledge to make decisions with imperfect information.
Impact of Chip Shortage
Unfortunately, every manufacturing company is dealing with a chip shortage right now. Our team is managing through this situation in partnership with customers and suppliers to navigate these challenging supply chain conditions, manage exceptions while working on mid and long-term mitigation plans.
Our team is leveraging our procurement power and excellent supplier relationships with our preferred partners to ease the situation for customers. We’ve defined clear roles and responsibilities from site buyers to managers to a dedicated worldwide escalation team and Global Commodity managers and use a range of tools to track progress. Our design teams are also working with customers on alternative designs and alternative components.
Building Supply Chain Transparency
One of the core competencies that has emerged from the past 18 months is the criticality of transparency into the supply chain. Supply chain professionals must have deep insights into component inventory, factory availability, and a myriad of other variables that go into delivering premium products to market quickly.
The value of supply chain transparency is highlighted in Flex’s COVID response early last year. Flex’s Pulse system helped our team quickly size and scope supply shortfalls and identified regional factory shutdowns to minimize disruptions to our customers. One of the most significant challenges supply chain professionals face is making difficult decisions with incomplete data. Thanks to Pulse and the experience of our supply chain professionals, we quickly understood the downstream effect of shortages and plant closures.
Supply chain transparency is often challenging to achieve for organizational reasons rather than technical ones. Many companies, including Flex, grow through acquisitions and must coordinate their operations and systems to create visibility for the supply chain team. We’ve made significant investments since 2015 to empower our team with enhanced transparency into components’ availability, location, price, and other variables utilizing a robust master data management program. Businesses lacking enhanced visibility into the supply chain may experience operations disruptions, a shortage (or overstock) of components, or product shipment delays impacting their bottom line.
Complete transparency is nearly impossible at this time but that shouldn’t dissuade supply chain professionals from striving to improve. The ability to gain a comprehensive understanding of component inventory, pricing, and location, is critical in a globally distributed supply chain. Without it, an already difficult job becomes near impossible.
Future Outlook
We’re in the midst of a historic time so it’s difficult to project when things will “settle down.” Successful vaccine rollouts throughout the world helped us achieve a small semblance of normalcy for a brief time but Delta and other COVID variants are spiking and causing unscheduled port closures, government lockdowns, and other challenges for premium brands. At this point, supply chain professionals must help businesses navigate a fluid global environment.
Imperatives for Building a Resilient Supply Chain
Risk mitigation measures must be embedded with clear accountability throughout the chain from procurement to last-mile delivery. One way to develop these measures is to consider the resilience dimensions that need to be continuously strengthened within your operation – and where along the chain they need greater reinforcement.
Flex believes flexibility, visibility, and collaboration are the key pillars to reinforce production and distribution systems. Multiple studies have found these to be among the leading attributes of resilient chains. Flexible organizations can adapt to disruptions with minimal impact. For example, one way to build flexibility is to develop multiple suppliers in the event of service interruptions by your primary suppliers.
When it comes to gaining visibility, this is absolutely critical to help anticipate risks in real time whether it’s understanding a weather event such as the path of a monsoon or the ESG reputation of a second-tier supplier. Finally, collaboration entails bringing together stakeholders to work towards a common goal, and this includes information-sharing both inside and outside of the organization. The stronger the collaboration between companies in a supply chain, the faster and more effectively they respond to disruptions.
The Move to Regionalized Supply Chain Hubs
We’ve spent the last decades learning how to manage global supply chains, primarily with Asia as a central hub. Industry pundits thought the volatility of the worldwide supply chain would lead many businesses to implement regionalization initiatives, but we haven’t seen that materialize in real-life just yet. The logic that premium brands want to build products closer to their customers to reduce freight and logistics risk is sound but it’s an extraordinarily large undertaking.
Supply chain professionals can’t re-locate their entire manufacturing, assembly, and freight operations to another region without disruptions. Premium brands must sink significant time and money to evaluate whether a regionalized supply chain would deliver value over time. There are also many additional variables, including constraints on cost and labor availability and the organization’s ability to manage the complexity of the transition and ramp-up without disturbing overall production. A return to a decentralized regional supply chain could remove layers of complexity and improve time to market, but there will also be cost increases.